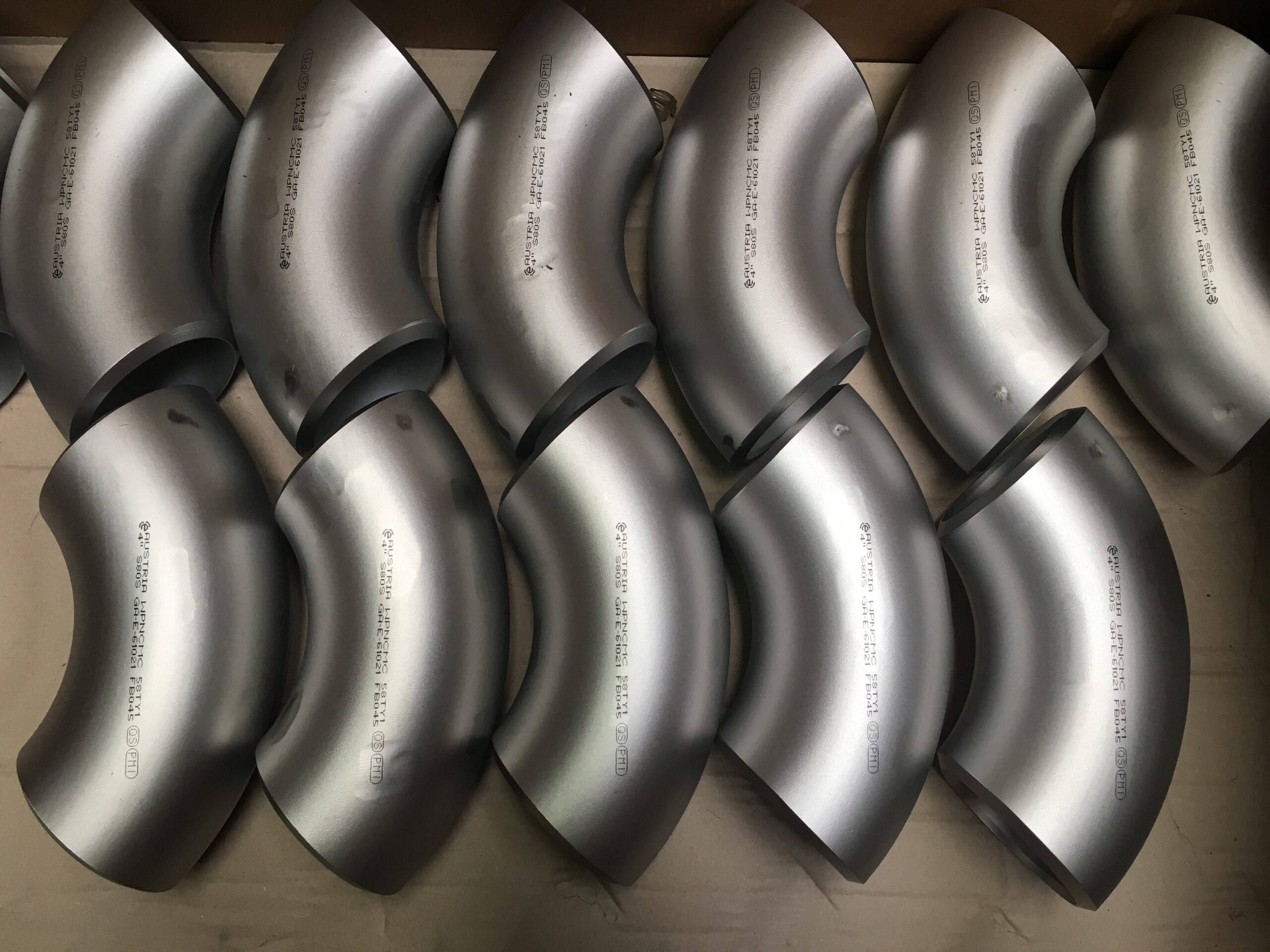
INCONEL 625
THE SAFE CONNECTION WITH INCONEL 625 FITTINGS FROM MÜRZZUSCHLAG
Erne Fittings uses cold forming to produce fittings at its plant in Mürzzuschlag, Austria. One special material they use there is UNS N06625, which is used predominantly for components at risk of corrosion.
UNS N06625, also known as Inconel 625, 2.4856 or NiCr22Mo9Nb is a nickel-chromium-molybdenum-niobium alloy that is highly resistant to corrosion. Due to its high strength and resistance to acids and alkalis, it can be used to create thin-walled components with good heat transfer.
Erne Fittings manufactures tees, elbows and reducers from UNS N06625, primarily with dimensions 2″ to 6″. The production options available in Mürzzuschlag do, however, also allow for dimensions 1/2″ to 12″., in some cases. Erne Fittings uses cold forming during its manufacturing process, as for all high-alloy materials. In contrast to hot forming, with this process there is no risk of any impact on the microstructure or surface quality due to the temperature profile during forming.
Another advantage of cold forming is that the same diameter can be used for both the pipe and the finished product. During the cold forming process, the workpiece is processed below the recrystallisation temperature. Intermediate annealing is sometimes necessary in cases of intense cold forming, prior to the final heat treatment taking place. UNS N06625 also has a higher level of cold work hardening compared to austenitic stainless steels, which has to be taken into account when choosing the forming device. Erne Fittings has all the experience and expertise it needs to process high-alloy materials at its Mürzzuschlag location.
UNS N06625 has a very high level of resistance to pitting, crevice and intercrystalling corrosion as well as considerable immunity against chlorine-induced stress corrosion. The material is used primarily for components exposed to seawater under high mechanical stress and for components at risk of corrosion used in a wide range of applications.
Erne News 01/2018